KUKA
![]() | This article contains promotional content. (July 2019) |
![]() | |
Company type | Subsidiary |
---|---|
Industry | Automation |
Founded | 1898 |
Headquarters | Augsburg, Bavaria, Germany |
Key people | Peter Mohnen (CEO and chairman)[1] |
Products | Industrial robots, automated production lines |
Revenue | €4.4 billion(2022) |
€118.4 million(2022) | |
€-42.6 million(2022) | |
Total assets | €2.58 billion(2022) |
Total equity | €3.9 billion(2022) |
Owner | Midea Group (95%) |
Number of employees | 15,000(2024) |
Divisions | |
Website | www |
![]() | |
Company type | GmbH |
---|---|
Industry | Machine systems and plant engineering, automation technology |
Founded | 1996 |
Founder | Johann Josef Keller and Jakob Knappich |
Headquarters | Augsburg, Germany |
Products | Plant engineering, special purpose machine manufacturing, automotive, automation technology, joining technology, engineering, photovoltaic industry, equipment manufacturing, press automation, forming technology, welding technology, control systems |
Revenue | €4.4 billion(2022) |
Number of employees | 15,000(2024) |
Parent | KUKA |
Website | www |
KUKA is a German manufacturer of industrial robots and factory automation systems. In 2016, the company was acquired by the Chinese appliance manufacturer Midea Group.[2]
It has 25 subsidiaries in countries including the United States, Australia, Canada, Mexico, Brazil, China, Japan, South Korea, Taiwan, India, Russia, and various European nations. KUKA is an acronym for Keller und Knappich Augsburg.
KUKA Systems GmbH, a division of KUKA, is a supplier of engineering services and automated manufacturing systems with around 3,900 employees in twelve countries globally.[3] KUKA Systems’ plants and equipment are used by automotive manufacturers such as BMW, GM, Chrysler, Ford, Volvo, Volkswagen, Daimler AG and Valmet Automotive, as well as by manufacturers from other industrial sectors such as Airbus, Astrium and Siemens. The range includes products and services for task automation in the industrial processing of metallic and non-metallic materials for various industries, including automotive, energy, aerospace, rail vehicles, and agricultural machinery.[4]
History
[edit]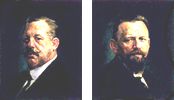
The acetylene factory Augsburg was founded in 1898 in Augsburg, Germany, by Johann Josef Keller and Jakob Knappich for the production of low-cost domestic and municipal lighting, household appliances, and automobile headlights. Their production extended into autonomous welding equipment in 1905.
After the First World War, Keller and Knappich resumed production of safety-winches, manual-winches, and power-winches and began manufacturing large containers. As a result, Bayerische Kesselwagen GmbH was formed in 1922. The new company developed and produced superstructures for municipal vehicles. In 1927, this business division presented the first large garbage truck.[citation needed] The name KUKA came into being in the same year through the company's name at that time, "Keller und Knappich Augsburg". In Hungary, the name—being prominently displayed on the first closed container garbage trucks—eventually became a generic trademark and ultimately a synonym for trash cans.[5][6]
Keller & Knappich GmbH merged with part of Industrie-Werke Karlsruhe AG to become Industrie-Werke Karlsruhe Augsburg Aktiengesellschaft, eventually shortened to KUKA (Keller und Knappich Augsburg).
The development and manufacture of spot welding equipment began in 1936. By 1939, KUKA had more than 1,000 employees.
Starting in 1934, KUKA expanded to become a major company. Its owners joined the NSDAP early on and benefited from the contacts this provided. The production of machine tools and machine components for the increasing demands of the arms industry, such as being an important supplier for Messerschmitt AG, and of anti-aircraft guns led to significant workforce expansion. The company had 1,000 employees in 1939, and this number steadily increased with the use of prisoners of war, “civilian workers,” and concentration camp prisoners. In 1944, 1,400 people working for “KUKA” were housed in Collective Camp II alone.[7]
After the major destruction of the company during the Second World War in 1945, KUKA resumed manufacturing welding machines and other small appliances. With new products such as the double-cylinder circular knitting machine and the portable typewriter "Princess," KUKA introduced new industrial fields and gained independence from the supply sector.[8]
In 1956, KUKA manufactured the first automatic welding system for refrigerators and washing machines and supplied the first multi-spot welding line to Volkswagen AG. Ten years later, the first friction welding machine went into production.
In 1971, the delivery of the first robotic welding system for the S-Class took place. A year later, the magnetic arc-welding machine came to market.
In 1973, KUKA created its own industrial robot, FAMULUS.[9][10] At that time, the company belonged to the Quandt group.
In 1980, the Quandt family withdrew and a publicly owned firm was established. In 1981, KUKA's main activities were grouped into three independent companies: KUKA Schweissanlagen und Roboter GmbH, KUKA Umwelttechnik GmbH and KUKA Wehrtechnik GmbH, which was re-sold to Rheinmetall in 1999. Towards the end of 1982, LSW Maschinenfabrik GmbH, Bremen became a subsidiary of KUKA.[11]
In 1993, the first laser-roof-seam welding systems were manufactured. These welding systems were then further expanded to adhesive bonding and sealing technologies in the following year. Around the same time, KUKA took over the tools and equipment manufacturers Schwarzenberg GmbH and expanded its business to China and the USA in the following years.
In 1995, the company was split into KUKA Robotics Corporation and KUKA Schweißanlagen (now KUKA Systems), both subsidiaries of KUKA AG. The company is a member of the Robotics Industries Association (RIA), the International Federation of Robotics (IFR), and the German engineering association VDMA.
In 1996, KUKA Schweissanlagen GmbH became an independent company and, two years later, became the leader among European welding equipment manufacturers. The supply of the first pressing tools for automobile side-walls made of high-strength steel began in 2002. The company launched the KUKA RoboScan with a remote laser welding head in 2003. Since 2006, KUKA Systems has operated its own body shell factory in Toledo, Ohio, producing the bodywork for the Jeep Wrangler by Chrysler.
In the course of internationalisation and expansion of business units and technologies such as reshaping, tooling, bonding, sealing, etc., KUKA Schweissanlagen GmbH became KUKA Systems GmbH in 2007. In 2010, KUKA presented a newly developed standardized cell concept for welding machines, KUKA flexibleCUBE.
In the automation sector, KUKA Systems offers standard and customized products for industrial production automation; joining technologies and component handling are among their activities. The technologies are tested, and the production processes are fully optimized before development. Additionally, KUKA Systems offers engineering and individual counseling.[12]
In June 2016, Midea Group offered to buy Kuka for about €4.5 billion ($5 billion). Midea completed the take over bid in January 2017 by purchasing the 94.55% voting stake in the company.[13]
In late 2017, Kuka announced that 250 employees of KUKA Systems were terminated. The management cited project troubles as the reason.[14]
Most robots are finished in "KUKA Orange" (the official corporate color) or black.
Corporate structure
[edit]The company is headquartered in Augsburg, Germany. As of December 2014, KUKA employed more than 13,000 workers.[15] While previously emphasizing customers in the automotive industry, the company has since expanded to other industries. It has five divisions:[16]
- Systems
- Robotics
- Swisslog Logistics Automation
- Swisslog Healthcare
- China[2]
Notable milestones
[edit]- 1971: Europe's first welding transfer line built for Daimler-Benz.
- 1973: The world's first industrial robot with six electromechanically driven axes, known as FAMULUS.
- 1976: IR 6/60 – A new robot type with six electromechanically driven axes and an offset wrist.
- 1989: A new generation of industrial robots is developed – brushless drive motors for low maintenance and higher technical availability.
- 2004: The first Cobot KUKA LBR 3 is released. This computer controlled lightweight robot can interact directly with humans without safety fences, resulting from a collaboration with the German Aerospace Center institute since 1995.[17]
- 2007: KUKA Titan – at the time, the biggest and strongest industrial robot with six axes, entered the Guinness Book of World Records.[18]
- 2010: The robot series KR QUANTEC completely covers the load range of 90 to 300 kg with a reach of up to 3100 mm.
- 2012: The new small robot series KR AGILUS is launched.
- 2014: The company gained recognition with a video supposedly teasing their new robot, specialized in Table Tennis, showing a match against Timo Boll, a German professional. The video, a commercial with heavy CGI, received criticism from the table tennis community but has been viewed over 10 million times on YouTube and has won numerous awards.[19]
- 2016: KUKA was acquired by the Chinese company Midea Group.[20]
- 2024: KUKA's next generation comes to Modex 2024.
System information and application areas
[edit]



System information
[edit]The KUKA system software is the operating software and the core of the entire control system. It contains all the basic functions needed for the deployment of the robot system.
Robots come with a control panel (the KCP, or KUKA Control Panel), also known as a teach pendant, which features a display and axis control buttons for A1-A6, as well as an integrated 6D mouse that allows the robot to be moved in manual (teaching) mode. The pendant also enables users to view and modify existing programs, as well as create new ones. To manually control the axes, an enabling switch (also called a dead man's switch) on the back of the pendant must be pressed halfway for motion to be possible. The connection to the controller is a proprietary video interface and CAN bus for the safety interlock system and button operation.
A rugged computer located in the control cabinet communicates with the robot system via the MFC,[21] which controls the real-time servo drive electronics. Servo position feedback is transmitted to the controller through the DSE-RDW/RDC[22] connection. The DSE[23] board is in the control cabinet, usually located on or integrated into the MFC, while the RDW/RDC board in located in the base of the robot.
The software comprises two elements running simultaneously: the user interface and program storage, which run on Windows 95 for KRC1 and early KRC2 controllers, Windows XP Embedded for KRC2 controllers, and Windows 7 Embedded for KRC4 controllers, as well as VxWin,[24] a KUKA-modified version of the VxWorks real-time OS for program control and motion planning, which communicates with the MFC.[21]
The systems also contain standard PC peripherals, such as a CD-ROM drive(or 3.5" floppy on older controllers), USB ports, as well as a standard interface, either ISA or PCI/PCIe, for adding software and hardware options for industrial automation, such as Profibus, Interbus, DeviceNet and Profinet, among others.
Fields of application
[edit]Aerospace
[edit]KUKA Systems supplied the TIG welding cell for the upper stage of the Ariane 5 launcher-rocket. TIG welding stands for tungsten inert gas welding and is a special form of arc welding, which is one of the core activities of KUKA Systems. The company also provides apparatuses and appliances for the construction of aircraft structural elements. Aerospace customers include Boeing, SpaceX, Bell and Airbus.
Automotive
[edit]The KUKA Systems portfolio includes a wide range of production automation solutions for joining and assembling vehicle body structures, from low-scale automated production facilities to highly flexible manufacturing systems. This includes the production of individual equipment or subassemblies to the assembly of complete body structures and mechanical parts. Equipment for assembling discs, mounting systems for vehicle bodies and chassis (so-called “marriage”), and component installation are also available.
BMW, GM, Chrysler, Ford, Volvo, Hyundai, Volkswagen, and Daimler AG are among the customers in this business sector.
Production of rail vehicles
[edit]Manufacturers of rail vehicles are also customers of KUKA Systems, for the construction of locomotives, subway wagons, or in setting up innovative and highly automated production lines for freight wagons.
Production of photovoltaic modules
[edit]KUKA Systems offers solutions for every step of photovoltaic module production, from brick-sawing to cell handling and cross-tie soldering to framing and packaging of modules.
Welding technology – General
[edit]KUKA Systems is active in various other industrial sectors as well. Examples include the production of baby strollers and the production of white goods for BSH (Bosch und Siemens Hausgeräte GmbH).
Awards and certificates
[edit]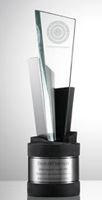
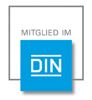
Certificates
[edit]Application areas
[edit]Industrial robots are employed across various sectors including material handling, machine loading and unloading, palletizing and depalletizing, spot and arc welding. They are prominently utilized by large enterprises, primarily in automotive and aerospace industries. Specific applications include:
- Transport industry: Used handling heavy loads, leveraging their load capacity and maneuverability.
- Food and beverage industry: Tasks include loading and unloading of packaging machines, meat cutting, stacking, palletizing, and quality control.
- Construction industry: Ensures smooth material flow.
- Glass industry: Applications range from thermal treatment of glass and quartz in laboratory settings to bending and forming operations.
- Foundry and forging industry: Robots are resistant to heat and dirt, enabling their use in and around casting machines for tasks like deburring, grinding, drilling, and for quality assurance.
- Wood industry: Applications include grinding, milling, drilling, sawing, palletizing, and sorting.
- Metal processing: Used in drilling, milling, sawing, bending, punching, as well as in welding, assembly, loading, and unloading operations.
- Stone processing: Industrial robots are employed in ceramic and stone industries for tasks like cutting and shaping. KUKA collaborates exclusively with BACA Systems to advance this technology.[26]
KUKA Entertainment
[edit]In 2001, KUKA partnered with RoboCoaster Ltd to develop the world's first passenger-carrying industrial robot. This robotic ride features roller coaster-style seats attached to robotic arms, offering programmable manoeuvres. Riders themselves can also program the motions of their ride. A second-generation system, the RoboCoaster G2, launched in 2010 at Universal's Islands of Adventure theme park in Orlando, Florida, enhances the experience with synchronized movements through attractions like Harry Potter and the Forbidden Journey's. The seats are mounted on robotic arms, which are then affixed to a track, enabling the arms to navigate through the attraction while synchronizing their movements with the show elements of the ride (including animated props, projection surfaces, etc.).[27][28][29][30]
KUKA's collaboration with RoboCoaster extends to Hollywood, with appearances in films such as Die Another Day, where KUKA robots depicted laser-wielding threats in an Iceland ice palace scene, and The Da Vinci Code, where a KUKA robot handed Robert Langdon a cryptex.
In 2007, KUKA introduced a simulator based on the Robocoaster,[31] featured in attractions like The Sum Of All Thrills ride at EPCOT in Lake Buena Vista, Florida.
Recently, KUKA robotic arms have been integrated into Royal Caribbean cruise liners' bionic bars. Users select drinks via tablet interface, with robotic arms mixing an array of spirits, mixers, and liqueurs to craft custom cocktails.
Gallery
[edit]-
1898 Company founded by Johann Josef Keller and Jacob Knappich
-
1949 an Augsburg Princess
-
1920 Success in large container construction
-
1931 Resistance Welding
-
1934 KdF Wagen
-
1955 Large container manufacture
-
1965 German-American tank program at KUKA
-
1972 Construction of the first Magnet-arc welding machine
-
1974 Seam welding
References
[edit]- ^ "Till Reuter terminates his office as CEO in December in agreement with the supervisory board – Peter Mohnen takes over and ensures continuity". KUKA. Retrieved 24 December 2018.
- ^ a b "China's Midea makes offer for German robotics group Kuka". Financial Times. 19 May 2016.
- ^ "KUKA Systems worldwide".
- ^ "KUKA Systems delivers to new Volkswagen plant". Retrieved 23 April 2010.
- ^ Tenczer, Gábor; Barakonyi (Képszerkesztő), Szabolcs (20 June 2020). "index.hu – Mi köze Kukának, a törpének a kukásautóhoz?" (in Hungarian). © 1999-2020 Index.hu Zrt. Retrieved 19 July 2020.
- ^ Nádasdy Ádám (18 September 2003). "A metonimikus szemétláda". Magyar Narancs. Retrieved 17 July 2022.
- ^ MASCHINENFABRIK KELLER & KNAPPICH GMBH (KUKA)
- ^ "Product distributor". Servo Supplier. Retrieved 8 June 2024.
- ^ Company history located on the KUKA Robotics Homepage
- ^ "History of Industrial Robots" (PDF). Archived from the original (PDF) on 24 December 2012. Retrieved 27 October 2012.
- ^ "Over 50 years of robotics expertise". KUKA AG (in Polish). Retrieved 8 June 2024.
- ^ "Company history located on the KUKA Systems Homepage". Retrieved 21 April 2010.
- ^ "China's Midea receives U.S. green light for Kuka takeover". Reuters. 30 December 2016.
- ^ "Local german newspaper". 17 November 2017. Retrieved 9 February 2018.
- ^ "Annual Report 2016" (PDF). KUKA. Archived from the original (PDF) on 14 January 2016. Retrieved 28 January 2018.
- ^ "Corporate structure". KUKA AG. Retrieved 31 December 2019.
- ^ "History of the DLR LWR". 17 March 2018.
- ^ Guinness World Records Ltd. (Hrsg.): Guinness World Records 2007. Bibliographic Institute, Mannheim, 2007. ISBN 978-3411140770
- ^ Press Release from 12 May 2015, Retrieved August 6th, 2015
- ^ "China's Midea Has 86% of Robot-Maker in $4.4 Billion Bid". Bloomberg.com. 20 July 2016.
- ^ a b Multi Function Card
- ^ Resolver Digital Converter
- ^ Digital Servo Electronics
- ^ "VxWin – Windows real-time platform". Retrieved 17 April 2019.
- ^ "Quality around the clock". Archived from the original on 19 July 2011. Retrieved 27 April 2010.
- ^ "Innovative solutions in the stone cutting industry: 100 robots for BACA Systems in North America". KUKA AG. Retrieved 8 September 2021.
- ^ Harry Potter World Orlando (22 March 2010). ""Harry Potter and the Forbidden Journey" Attraction Details". Harry Potter World Orlando. Retrieved 24 January 2014.
{{cite web}}
: CS1 maint: numeric names: authors list (link) - ^ Kuka Entertainment. "Kuka Entertainment – Robocoaster". Kuka Entertainment. Archived from the original on 7 August 2010. Retrieved 29 June 2010.
- ^ Kuka Industrial Robots. "Kuka Industrial Robots – Robocoaster". Kuka Industrial Robots. Archived from the original on 30 May 2010. Retrieved 29 June 2010.
- ^ Robocoaster (22 March 2010). "Large & Theme Park Solutions". Robocoaster. Retrieved 29 June 2010.
{{cite web}}
: CS1 maint: numeric names: authors list (link) - ^ "KUKA Entertainment 4D Simulator". Retrieved 11 January 2008.
- Companies based in Bavaria
- Companies based in Augsburg
- Robotics companies of Germany
- Robotics companies of China
- Multinational companies headquartered in China
- Manufacturing companies established in 1898
- Engineering companies of Germany
- Engineering companies of China
- Industrial robotics companies
- Industrial machine manufacturers
- Amusement ride manufacturers
- 1898 establishments in Germany
- 2016 mergers and acquisitions
- Manufacturers of industrial automation
- Quandt family
- Midea Group