Draft:Grinding burn
Submission declined on 5 August 2024 by Garsh2 (talk). This submission is not adequately supported by reliable sources. Reliable sources are required so that information can be verified. If you need help with referencing, please see Referencing for beginners and Citing sources.
Where to get help
How to improve a draft
You can also browse Wikipedia:Featured articles and Wikipedia:Good articles to find examples of Wikipedia's best writing on topics similar to your proposed article. Improving your odds of a speedy review To improve your odds of a faster review, tag your draft with relevant WikiProject tags using the button below. This will let reviewers know a new draft has been submitted in their area of interest. For instance, if you wrote about a female astronomer, you would want to add the Biography, Astronomy, and Women scientists tags. Editor resources
| ![]() |
Submission declined on 3 November 2023 by Voorts (talk). This submission is not adequately supported by reliable sources. Reliable sources are required so that information can be verified. If you need help with referencing, please see Referencing for beginners and Citing sources. Declined by Voorts 13 months ago. | ![]() |
Comment: Large sections of the article remain unsourced. Some reliable sources are listed but not included as in line citations. (See WP:ILC) Garsh (talk) 18:38, 5 August 2024 (UTC)
Comment: The sources listed in the references are all unreliable because they're company websites selling a product or testing. Brinksmeier et al. and Karpuschewski et al. appear to be reliable sources, but there's no citations to them in the article body so it's unclear what information they're substantiating. voorts (talk/contributions) 21:01, 3 November 2023 (UTC)
![]() | An editor has marked this as a promising draft and requests that, should it go unedited for six months, G13 deletion be postponed, either by making a dummy/minor edit to the page, or by improving and submitting it for review. Last edited by Garsh2 (talk | contribs) 4 months ago. (Update) | ![]() |
Grinding burn is the term used to describe structural and residual stress changes that occur during grinding due to thermal overload.

Basics
[edit]During mechanical processing of steels, heat is generated which is introduced into the component. This heat input can lead to irreversible changes in the structure and microstructure as well as to resulting residual stress changes, especially in surface near areas of the component [1][2][3]. This effect is called thermal overload.
Similar damage may also caused by other mechanical machining processes, such as hard turning. The heat-induced processes in the material are basically the same here as during grinding. But the "burns" possible in this process differ in their severity from the actual grinding burn due to the used tools. Therefore the structural changes should be named after the machining process that caused them, in the case of hard turning as turning burn.
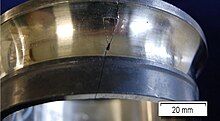
Grinding burn can occur in the form of tempered zones and, with even higher heat input, in the form of re-hardened zones (Fig. 1). It is also possible that grinding burn does not manifest itself through structural changes visible under the optical microscope, but only through changes in residual stresses.
A prerequisite for the development of grinding burn is the property of the material used to form a martensitic microstructure. Grinding burn cannot therefore occur in high-alloy austenitic steels and high-alloy ferritic steels. The carbon content in the steel must be high enough to allow martensite to form during rapid cooling. This is the case from a carbon content above 0.3% by mass.

The structural and residual stress changes caused by grinding burn lead to locally altered component properties and reduce its service life and long-term stability. Figure 2 shows a case of damage to a rolling bearing inner ring caused by grinding burn. The detailed image of the raceway surface shows a crack network (Fig. 3). The metallographic cross-section clearly shows the trigger for the crack formation: severe grinding burn with rehardening zones and tempering zones (Fig. 4).
Detection / testing of grinding burn
[edit]Grinding burn can be seen with the naked eye only on very severely damaged workpieces. Then blue to black discolorations form on the component caused by oxidation of the surface, so-called tempering colors. However, this is usually not the case. For this reason, various methods of grinding burn testing have been developed to detect grinding burn in or on the surface of a component.
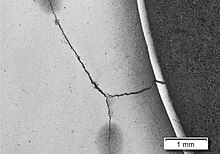
The oldest method is abrasive burn etching, also called nital etching (US standard AGMA 2007-B92, AMS 2649, ISO 14104). Grinding burn etching causes a chemical change in the component surface and discoloration remains. In addition, the process is difficult to automate. For this reason, non-destructive testing methods for the detection of grinding burns, such as the Barkhausen noise method and eddy current testing have become established in recent years.
More information
[edit]- Application of Surface Temper Etching[4]
- Manufacturing of referernce blocks with artificial defects[4]
- Application of Barkhausen noise method[5]
- Application of eddy current testing[6][7]
References
[edit]- ^ Seidel, Martin W.; Zösch, Antje; Härtel, Konstantin (2020). Grinding burn and its testing. A guide for the practice. imq Ingenieurbetrieb GmbH. ISBN 978-3-00-070194-8.
- ^ Karpuschewski, B. (2008). "Gear finishing by abrasive processes". CIRP Annals. 57 (2): 621–640. doi:10.1016/j.cirp.2008.09.002.
- ^ Brinksmeier, E.; Heinzel, C.; Wittmann, M. (1999). "Friction, Cooling and Lubrication in Grinding". CIRP Annals - Manufacturing Technology. 48 (2): 581–598. doi:10.1016/S0007-8506(07)63236-3.
- ^ a b "Grinding burn: Basics and detection". imq-Ingenieurbetrieb GmbH. 2024.
- ^ "Grinding Burn Detection". Stresstech. Retrieved 2023-08-07.
- ^ "Crack and grinder burn masters · ibg Eddy Current Technology, Test Instruments, Probes and Coils". ibg Eddy Current Technology, Test Instruments, Probes and Coils (in German). Retrieved 2023-08-07.
- ^ "Products". CNS GmbH (in German). Retrieved 2023-08-07.